Provision for appropriate and affordable housing is a significant challenge in both emerging and industrialized countries. Conventional constructions in dense urban, rural, or remote areas put enormous pressure on cost and resource efficiency. It captivates the private and government sector construction industries. Modular houses or pre-fab houses can offer great opportunities for both environmental and economic performances. It is emerging as the most cost-effective and attractive alternative to on-site constructions.
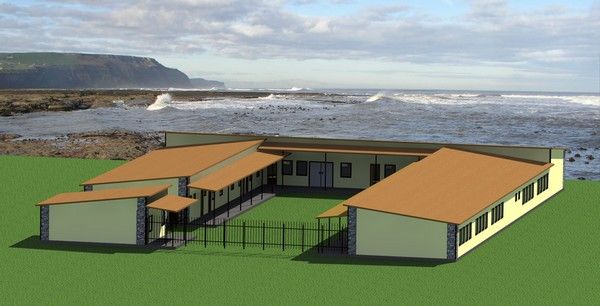
The modular houses or pre-fab houses create a good market share in the prefabrication industry. Its overall construction output remains prevalent in most developing countries, including Australia. In order to enhance the profile of prefab housing and effectively improve high performance, sustainable, and affordable housing, it is essential to understand and study the needs and perceptions of the construction projects adequately.
Recent investment in Australia’s housing sector has boosted many prospects for modular housing. Australia’s most prominent house builders entered a venture with the reputed Modular house manufacturer’s to build thousands of modular homes across the country. The modular houses or pre-fab houses seem as speedier new construction methods and the best way to fix the housing crisis in Australia.
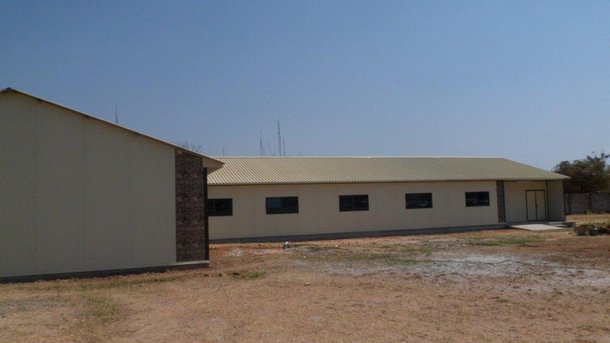
Modular housing is on the edge of a significant milestone. It is a construction method under which houses or blocks of flats are built in sections offsite in a factory. Factory-built housing systems are proved to speed up the construction process and construction efficiency. It seems as a sector that’s been singularly resistant to any modernization and could make things more efficient and bring down the building costs as well.
The pressures on traditional construction contractors or builders to meet the demand are slowing down due to several reasons. The modular houses or pre-fab houses option makes them adopt such new methods of construction. It is likely to drive innovation in construction methods and establishes a real change in the construction industry. Furthermore, the factory-built modular houses or pre-fab houses not only require less labor, but they can also be built much faster than traditional homes.
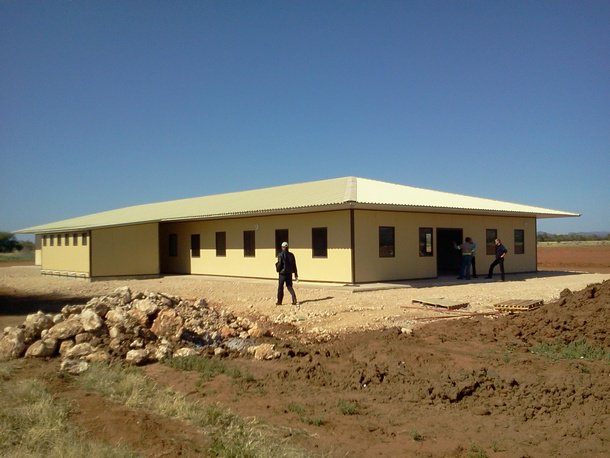
Conventional builders produce homes to sell them to protect their profit margins. This is why modular housing or pre-fab houses has been used primarily for affordable housing schemes, hotels, or properties in the rental market. It has the advantage of being constructed indoors in a controlled environment instead of a building site and exposed to several elements. The speed of manufacturing the structure takes less than a week to build in a factory and is easy to transport to the construction site.
Each part of modular houses or pre-fab houses is designed as per the need of the client. They are thoroughly checked with the advanced digital quality control system that follows every process in the factory. It leaves with zero defects, unlike traditional constructions. The modular or pre-fab houses have a lower carbon footprint because there are fewer lorry deliveries to the site, cutting emissions. Also, it produces less noise, pollution, and disruption for people living nearby!
For a faster construction, low waste, environmentally friendly construction process contact Aussie Panel at +61 (0) 411867333 today! They give you an option to enjoy creative accommodation with comfort and low price without sacrificing the quality of your building structure.
0 comments:
Post a Comment